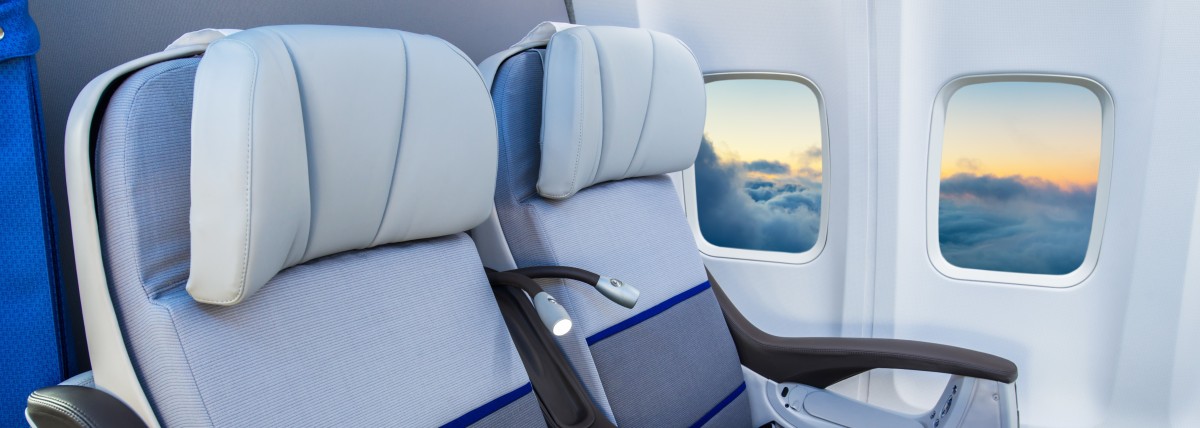
Die richtige Nadel in der Produktion von Sitzmöbeln für Kraft- und Luftfahrzeuge, Schiffe und Züge
Fahrzeugsitze müssen vielfache Anforderungen erfüllen. In erster Linie sind Fahrzeugsitze sicherheitstechnische Produkte, bei denen Aspekte wie Flamm- und Lichtbeständigkeit, Dehnung des textilen Flächengebildes sowie Scher- und Scheuerfestigkeit eine maßgebliche Rolle spielen. Die sicherheitstechnische und funktionelle Qualität der Sitze steht deshalb bei der Fertigung an erster Stelle.
Typische Verarbeitungsprobleme
Sitzbezüge werden überwiegend aus schaumstoffkaschierten Gewebe- oder Maschenwaren genäht, wobei sich die Schaumstoffkaschierung in Festigkeit und in Materialhöhe (1-10mm) unterscheidet und sich genau wie die Ausrüstung entscheidend auf die spätere Vernähbarkeit auswirkt. Man spricht hier von Composites, da die Polstermaterialien der Sitze meist aus drei Lagen bestehen: Material der Warenoberseite, Schaumstoff und Wirkware als Warenunterseite.
Typische Nähprobleme bei der Autositzfertigung sind in erster Linie:
- Fehlstiche und Nadelbruch
- Thermische Schäden
- Materialbeschädigungen
A. Fehlstiche, Nadelbruch und die Lösung
Drei Ursachen für Fehlstiche bei der Verarbeitung von Fahrzeugsitzen:
1. Unterschiedliche Materiallagenhöhen
Die dünneren Materiallagen flattern unter dem Presserfuß. Die Materiallagen, die nicht vom Presserfuß gehalten werden, bewegen sich beim Aufwärtshub der Nadel zusammen mit der Nadel nach oben und verkleinern so die Fadenschlinge. Es erfolgt keine oder nur minimale Schlingenbildung, der Greifer kann die Schlinge nicht mehr erfassen.
2. Kreuznähte/ Quernähte
In diesem Fall entsteht das Flattern durch die Übergänge von hohen zu niedrigen (bzw. niedrigen zu hohen) Materiallagen. Auch hier wird die Nadelfadenschlinge von den Materiallagen verkleinert, die nicht vom Presserfuß gehalten werden, sodass der Greifer die Schlinge nicht mehr erfassen kann.
3. Nadelauslenkung
Eine weitere Ursache für Fehlstiche ist die Auslenkung der Nadel bei extrem dicken Materiallagenübergängen, wodurch die Aufnahme der Fadenschlinge durch den Greifer ebenfalls beeinträchtigt wird.
Ursache für Nadelbruch in der Produktion von Fahrzeugsitzen:
Große Nadelauslenkung
Durch extrem dicke Materiallagenübergängen, z.B. beim Übernähen von Quernähten, wird die Nadel von ihrer korrekten, geraden Einstichbahn abgelenkt. Beim Kontakt der Nadelspitze mit dem Greifer oder anderen Maschinenteilen bricht die Nadel.
Hier bietet SCHMETZ eine Lösung: die SERV 7 Nadel
Die SERV 7 Nadel zeichnet sich durch einen konisch verstärkten Nadelschaft für höhere Nadelstabilität und zur Vermeidung von Fehlstichen aus. Des Weiteren trägt die optimierte Hohlkehlform zur sicheren Schlingenbildung und zur Vermeidung von Fehlstichen selbst unter extremen Nähbedingungen bei.
Anwendungsbereiche in der Herstellung von Fahrzeugsitzen:
- Sitzbezüge für Verkehrsmittel (Auto, Flugzeug, Bahn, etc.)
- Kopfstützen
- Kaschierte Textilien
- Materialkombinationen, z.B. Textil und Kunststoffprofile, Textil und Pappe
- Hohe und feste Materiallagen
B. Thermische Beschädigungen und die Lösung
In der Sitzfertigung werden in der Regel keine hohen Nähgeschwindigkeiten eingesetzt. Der Schaumstoff, der auf die Materialunterseite kaschiert wird, lässt nur reduzierte Drehzahlen im Bereich 1.500 bis max. 3.500 Stichen/min. zu. Aber auch geschäumte Plastikschienen aus Polyurethan (PU) oder andere Materialien aus Kunststoff lassen sich nur mit verminderter Nähgeschwindigkeit beschädigungsfrei verarbeiten. Werden die Nähgeschwindigkeiten überschritten, treten thermische Schäden in Form von Nadelverklebungen und Zusammenkleben der Materiallagen auf. Die physikalischen Eigenschaften der Schaumstoff-Kunststoff-Materialien (Schmelzpunkt von ca. 170 – 235° C) geben die Nähgeschwindigkeit vor.
Zusammenkleben der Materiallagen
Bei überhöhten Nähgeschwindigkeiten entstehen durch die niedrigen Schmelzpunkte der Materialien thermische Schäden: angeschmolzenes Material im Einstichloch, Nadelverklebung und -verschmierung bis hin zu völligem Nadelöhrverschluss mit Fehlstichen und Fadenbruch als Folge. Die Ursache dieser Schwierigkeiten ist immer, dass Nähgutbestandteile schmelzen und sich an der Nadel festsetzen. Solange sich die Nadel noch in der Arbeit befindet, bleiben diese an der Nadel klebenden Rückstände plastisch verformbar und erhöhen die Reibung zwischen Nadel und Nähgut beträchtlich. Wird die Maschine angehalten, kühlt die Nadel sofort ab, die geschmolzenen Rückstände werden hart und machen eine Weiterverwendung der Nadel auf Dauer unmöglich.
Hier bietet SCHMETZ eine Lösung: Nadeln mit NIT-Beschichtung
Beim außenstromlosen Vernickeln, auch als chemisches Vernickeln bekannt, wird in der Elektrolytlösung PTFE (Polytetrafluorethylen) dispergiert, das sich zusammen mit der Nickel-Phosphor-Schicht auf den zu beschichteten Nadeln abscheidet. Dadurch erhalten NIT-Nadeln ganz besondere Eigenschaften .
Anwendungsbereiche in der Herstellung von Fahrzeugsitzen:
- Materialien mit flammhemmender Ausrüstung
- Synthetische Materialien
- Materialien mit hohem synthetischen Anteil
Die NIT-Beschichtung hält bei flammhemmend ausgerüsteten Stoffen länger als alle anderen auf dem Markt befindlichen Beschichtungen (z. B. Titannitrid). Beim Nähprozess wird durch die Verwendung beschichteter Nadeln allerdings NICHT die Nadeltemperatur reduziert, wie fälschlicherweise meist angenommen wird. Synthetische Materialien werden beim Überschreiten ihres Schmelzpunktes im Einstichlochbereich durch die Nadeltemperatur angeschmolzen, was zu Materialbeschädigungen führen kann. Die Nadel selbst bleibt jedoch frei von „Verklebungen“. Auch beim Einsatz einer beschichteten Nadel muss, um Materialbeschädigungen durch zu starke Reibung und damit hohe Nadeltemperaturen zu vermeiden, die Nadeldicke auf das Material abgestimmt und eventuell die Nähgeschwindigkeit reduziert werden.
Dabei ist zu beachten, dass die NIT-Nadel bei der Verarbeitung von hellen Materialien vor Eingabe der Nadeln in die Produktion unbedingt „abgenäht“ werden sollte. Das heißt, die äußere Schicht wird auf ca. 50 cm Nahtlänge an den Stichlochrändern abgestreift, und es werden „farbige“ Einstichpunkte erkennbar. Durch das Abnähen erhalten die Nadeln ein helleres Aussehen, das jedoch nicht zu einer Beeinträchtigung der Funktions- und Gebrauchstüchtigkeit führt.
C. Materialbeschädigungen und die Lösung
In der Produktion von Fahrzeugsitzen sind Materialbeschädigungen ein häufig auftretendes Problem. Neben dem Einsatz zu hoher Nadeldicken in der Fertigung ist eine weitere Hauptursache für Beschädigungen der Einsatz ungeeigneter Nadelspitzenformen.
SCHMETZ bietet Ihnen zwei unterschiedliche Arten von Nadelspitzen an: Kugel- bzw. Rundspitzen und Schneidspitzen.
Folgende Kugel- bzw. Rundspitzen stehen für Sie zur Auswahl:
Hier bietet SCHMETZ eine Lösung: Rund- und Kugelspitzen R , SES und SUK
Die R-Spitze ist die Standardspitzenform und verfügt über ein breites Einsatzspektrum. Treten jedoch Beschädigungen durch An- oder Druchstechen von Materialfäden insbesondere von Maschenwaren auf, sollte die SES- oder SUK-Spitze verwendet werden.
Anwendungsbereiche in der Herstellung von Fahrzeugsitzen:
R:
- Gewebe und Schaumstoffkaschierungen
- Materialkombinationen
- Festere Lederqualitäten, die mit der normalen R-Spitze noch problemlos zu durchstechen sind
SES:
Feine bis mittlere Maschenware und Schaumstoffkaschierungen
SUK:
Grobe Maschenware und Schaumstoffkaschierungen
Der Nutzen der Kugelspitzen SES und SUK:
- Höhere Verdränungswirkung im Vergleich mit der R-Spitze
- Geringere Nadeleinstichkräfte als die R-Spitze
Je dichter das Nähgut ist und je mehr Lagen miteinander vernäht werden müssen, umso weniger Platz ist für den Einstich der Nadel zwischen den Materialfäden und umso höher wird die Gefahr, dass ein Materialfaden von der Nadel „angestochen“ wird.
Beim „Anstechen“ eines Fadens wird entweder der ganze Faden oder aber einige Fasern verletzt. Diese Beschädigungen sind zunächst vielleicht nicht mit bloßem Auge sichtbar. Doch durch mechanische Beanspruchung werden diese Schäden verstärkt und treten deutlich hervor. Deshalb ist die Verdrängungswirkung der Kugelspitze umso sinnvoller und wichtiger, je kleiner die Zwischenräume zwischen den einzelnen Materialfäden sind. Ein weiterer „Nebeneffekt“ des Einstechens in die Material-Zwischenräume ist eine Verringerung der Nadeleinstichkräfte, wodurch auch bei hohen Lagenzahlen weniger Nadelbruch entsteht.
Ein Vergleich verschiedener Nadeldicken zeigt, dass die Nadeleinstichkräfte dünnerer Nadeln deutlich geringer sind. Dies korreliert mit weniger Beschädigungen am Nähgut und minimiert aufgrund geringerer Reibung auch thermische Schäden. Ebenfalls sind die Nadeleinstichkräfte bei Verwendung von Kugelspitzen kleiner als bei Verwendung der normalen Rundspitze.
Hinweis: Nach jedem Schichtwechsel – oder in Abhängigkeit von der Beanspruchung auch in kürzeren Intervallen – empfehlen wir Ihnen das Auswechseln der Nadeln, um eine Materialbeschädigung durch defekte Nadelspitzen zu vermeiden.
Tipp: Wählt man die Nadel in SERV 7 -Ausführung eine Nadeldicke geringer als die Standard-Ausführung, so erhält man kleinere Einstichlöcher und damit weniger Materialbeschädigungen bei gleicher Nadelstabilität.
Anforderungen an Schneidwirkung und Nahtoptik
Im Bereich Fahrzeugsitze werden oft Verbundstoffe, z. B. kaschiertes Material zusammen mit Kunststoffprofilen, aber auch Leder verarbeitet. Hier bietet sich die Verwendung von Nadeln an, deren Spitzen Schneidkanten haben. Diese speziellen Nadeln durchdringen das Nähgut aufgrund ihres Schneidvermögens leichter bei geringerer Erwärmung der Nadel. SCHMETZ bietet eine große Auswahl verschiedener Schneidspitzen an. Die Bestimmung der optimalen Spitzenform ist abhängig von der Materialdicke, der Nahtart und -funktion und auch von der beabsichtigten Nahtoptik. Einstichloch und Nahtbild variieren, je nachdem, ob der Querschnitt der Schneide linsenförmig, rautenförmig oder dreieckig ist. Weiterhin spielt es eine Rolle, ob er quer, schräg oder in Nahtrichtung liegt.
Hier bietet SCHMETZ eine Lösung: spezielle Schneidspitzenformen
Die Schneidspitzenformen LR, LL, S, P, PCL und PCR sind für alle Lederarten geeignet, die in der Herstellung von Fahrzeugsitzen verwendet werden. Der Hauptgrund für den Einsatz dieser Schneidspitzen ist die Erzielung einer bestimmten Nahtoptik.
Anwendung der Schneidspitzen LR, LL, S, P, PCL and PCR in der Verarbeitung von Fahrzeugsitzen:
- Diese Spitzenformen sind für alle Lederarten geeignet, die in der Herstellung von Fahrzeugsitzen verwendet werden.
- Die LR-Spitze wird verwendet, wenn eine dekorative Nahtoptik mit leicht nach links geneigten Stichen gewünscht wird. Eine Stichdichte bis zu 5 – 6 Stichen/cm ist möglich.
- Die LL-Spitze erzeugt eine Naht mit geraden Stichen, die leicht eingezogen sind. Die Naht ist resistenter als die mit einer S-Spitze, die Stiche aber nicht ganz so gleichmäßig. Eine Stichdichte von 5 – 6 Stichen/cm ist möglich.
- Die S-Spitze bewirkt eine sehr gerade Nahtlinie. Der Nähfaden wird in das Leder eingezogen. Die S-Spitze wird häufig zur Erstellung von Grobziernähten eingesetzt, wo mit dicken Nähfäden und großen Stichabständen gearbeitet wird. Aufgrund des Einschnitts in Nahtrichtung sollte eine Stichdichte von 3 – 4 Stichen/cm nicht unterschritten werden, um eine Perforation der Naht zu vermeiden.
- Die P-Spitze wird besonders für Nähte verwendet, die großen Belastungen ausgesetzt sind. Eine Stichdichte von 6-8 Stichen ist möglich.
- Die PCL- und PCR-Spitze sollten zum Schutz des Nähfadens gewählt werden, wenn festes, hartes Leder verarbeitet wird. Bei von links nach rechts eingefädelten Nadeln muss immer die PCL eingesetzt werden. Die PCR wird insbesondere als linke Nadel in einer Zweinadelmaschine eingesetzt.
Hier bietet SCHMETZ eine Lösung: spezielle Schneidspitzenformen
Für die Sitzfertigung stehen Ihnen drei verschiedene Arten von Dreikantschneiden mit abgestufter Schneidwirkung zur Verfügung. Alle drei erzeugen eine Naht mit gerade liegenden Stichen.
Anwendung der Dreikantschneiden D, DH und SD1 in der Produktion von Fahrzeugsitzen:
- Nadeln mit Dreikantspitzen D und DH werden speziell bei Kombinationen von Leder, Textil oder synthetischen Materialien in Verbindung mit Plastikprofilen oder Pappmaterial besonders fester Qualität eingesetzt. Die Stichdichte sollte nicht mehr als 3-4 Stiche/cm betragen.
- Die Rundspitze mit kleiner Dreikantschneide SD1 ist für den Einsatz beim Vernähen von Materialkombinationen mit eher weichem Kunststoffmaterial geeignet. Es sind Stichabstände bis hin zu 6-8 Stichen/cm möglich.
- Die SD1 ist auch für das multidirektionale Nähen bei Leder geeignet, da die Stichlage in allen Nährichtungen gleich bleibt.
- Je härter und trockener das Leder ist, desto mehr Schneidwirkung ist erforderlich: SD1-Spitze mit ca. 10 % Schneidwirkung, DH-Spitze mit ca. 50 % Schneidwirkung, D-Spitze mit ca. 90 % Schneidwirkung.
- Dreikantspitzen bilden in der Regel einen sehr geraden Stich.
Tipp: Bei hohen Anforderungen an die Stabilität der Nadel empfehlen wir die SD1-Spitze in Verbindung mit dem SCHMETZ SERV 7-Design. Die Verstärkung im Schaftbereich wirkt Nadelbruch entgegen und die Höckerhohlkehle verhindert Fehlstiche.
Achtung: Bei zunehmender Schneidwirkung ist beim Anfangs- und Endriegeln mit Beschädigungen des Nähfadens bzw. des Materials zu rechnen. Die Verriegelung sollte nicht in der Nahtlinie erfolgen sondern seitlich zur Naht:
Hinweis: Abhängig von der Materialstruktur und Anzahl der Lagen sollten bei der Verarbeitung von vorwiegend textilem Material Rund- bzw. Kugelspitzen verwendet werden. Schneidspitzen sind hauptsächlich für die Lederverarbeitung geeignet, zum Teil auch für die Verarbeitung von Materialkombinationen mit Kunststoff oder Pappe. Dabei ist allerdings zu beachten, dass die textilen Nähgutbestandteile durch die Schneidspitze beschädigt werden können. Für die optimale Auswahl sollte die Spitzenform individuell in Versuchen auf das vorliegende Material bzw. den Materialmix und die Verarbeitungstechnik abgestimmt werden.
Info: Spezielle Nadelsysteme 134-35 FL SERV 7 und 134-35 FK-E SERV 7 in der Fahrzeugindustrie
Für das im Bereich der Sitzfertigung meistgenutzte Nadelsystem 134-35 hält SCHMETZ eine spezielle Variante bereit: das Flachkolben-Programm. Es wird mit der Zusatzbezeichnung FL oder FK-E gekennzeichnet und ist eine SERV 7-Ausführung.
Der Nutzen der 134-35 FL SERV 7 und 134-35 FK-E SERV 7:
Durch den abgeflachten Kolben wird die Nadel immer in exakt der gleichen Position in der Nadelstange befestigt und kann nicht verdreht eingesetzt werden. Dadurch ist die geforderte Reproduzierbarkeit sicher gestellt und die Nähte werden in gleichbleibender Qualität gefertigt.