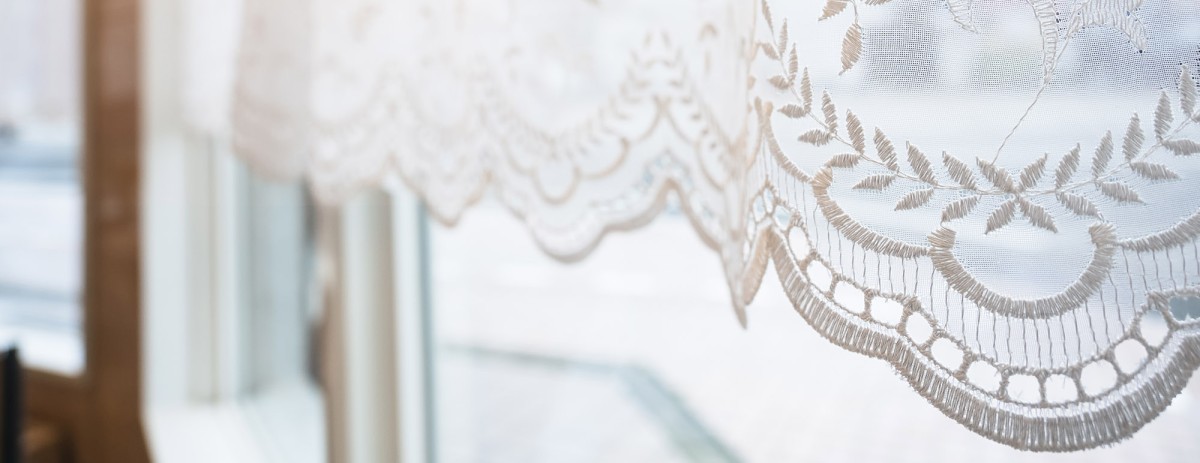
SCHMETZ Schiffli Needles - The perfect needles for perfect Schiffli embroidery results
Schiffli embroidery is a Swiss invention; “Schiffli” is the Swiss word for shuttle. In the year 1863, Isaak Gröbli developed the first Schiffli embroidery machine in the Swiss town St. Gallen.
Nowadays Schiffli embroidery is manufactured primarily in Asia and in Turkey. The required machines are produced mainly in Switzerland.
Schiffli embroidery is used to create high-quality products . It is applied in the field of exclusive clothing, such as lace for underwear, bridal and evening wear, and in the field of home textiles, e.g. for curtains, tablecloths and other home accessories.
In the manufacture of Schiffli embroidery, you have to consider many parameters. Only if you accurately coordinate all parameters you will receive a perfect Schiffli embroidery of high quality. Therefore, to ensure a smooth and flawless production, you have to carefully adjust and regularly check all embroidery parameters that influence your production: material, needle, thread and machine settings. If you change one parameter, you should absolutely check the others.
Special needle systems for Schiffli embroidery
Today, apart from some very special types, there are mainly two different Schiffli systems in use. Experts distinguish between two fundamentally different machine types and needle systems:
- Needles for Schiffli machines of the Plauen system
- Needles for Schiffli machines of the Saurer system
The main differences between the mentioned needle systems is the position (angle) of the flat area of the shank with reference to the threading direction as well as the shank diameter of the needle. For both systems (Plauen and Saurer) there are not only needles for normal embroidery machines, where all needles are fixed in one needle holder, but also needles for embroidery machines with color change, where each needle is fixed in its own needle holder. The only difference between the two needle variants is the shank diameter. The needle designation does not have an "S" for "Schiffli" but is preceded by a "0", e.g. 854 S for normal machines and 0854 for color change machines. The position of the flat area of the shank, the needle length from the butt to the beginning of the eye as well as the total length of the needle are identical.
Needle system 854 S of the Plauen system
This needle system is used in Schiffli machines of the Plauen system; system 854 S for normal machines and system 0854 for color change machines. The butt-to-eye length of needle system 854 S TOP is 4 mm longer. This is why they are used for machines with larger TOP shuttles.
Application in the Schiffli industry: for Schiffli machines of the Plauen system, made by Zangs (Germany), Hiraoka (Japan), Comerio Ercole (Italy), Metalmeccanica (Italy), Wems (Japan)
Needle system 110 S of the Saurer system
This needle system is used in Schiffli machines of the Saurer system; system 110 S in normal machines, system 0110 in color change machines and system 110 S TOP in machines with TOP shuttles.
Application in the Schiffli industry: for Schiffli machines of the Saurer system, made by Saurer, Lässer (Switzerland)
Needle system L 83 TOP of the Lässer system
Needle system L 83 TOP is used in machines made by Lässer (Switzerland). This system combines the threading direction (and therefore the flat area of the shank) of the Plauen system (854 S) and the shank diameter of the Saurer system (110 S). This system is only produced in TOP version. Therefore, it is often simply called L 83.
Application in the Schiffli industry: for Lässer Schiffli machines
Find the right needle to avoid material damage using special point shapes
The "NORMAL" R point
The advantages of the R point:
- Best for noncritical fabrics
- Exact penetration even with dense materials
- Accurate border lines of embroidery
The “NORMAL” R point is a very slim round point. You normally use the standard R point on noncritical woven fabrics and nonwovens, where an exact penetration of materials is required. Should, however, damages occur as a result of piercing fabric threads, we recommend to use the medium ball point SUK or for coarser base material the special point for embroidery STR.
The medium ball point SUK
The advantages of the SUK point:
- Best for knitted fabrics
- Increased displacement effect compared to the R point
- Lower penetration force than the R point
- Prevention of material damage
The medium ball point SUK is slightly rounded. The rounded point displaces the material threads and penetrates the fabric without damaging it. Therefore, the SUK ball point is particularly suitable for fine knitted fabric or tulle.
The special ball point STR
The advantages of the STR point:
- Best for coarse tulle or net fabrics
- Increased displacement effect compared to the SUK point
- Lower penetration force than the SUK point
- Prevention of material damage
The special ball point STR for embroidery is more rounded than the medium ball point SUK and increases the displacement effect even more than an "SUK" point. We recommend to use an STR point for extremely coarse materials such as net fabric or coarse knitted fabrics and when thicker material threads need to be displaced during the penetration to avoid material damage.
Color coding – needle identification made easy
For a quick and easy identification of the needle size and point shape, SCHMETZ Schiffli needles are provided with a color code. It is printed on the flat part of the shank. Thanks to the color code, the machine operator can see at a glance whether all needles in the machine have the same characteristics in terms of needle size and point shape.
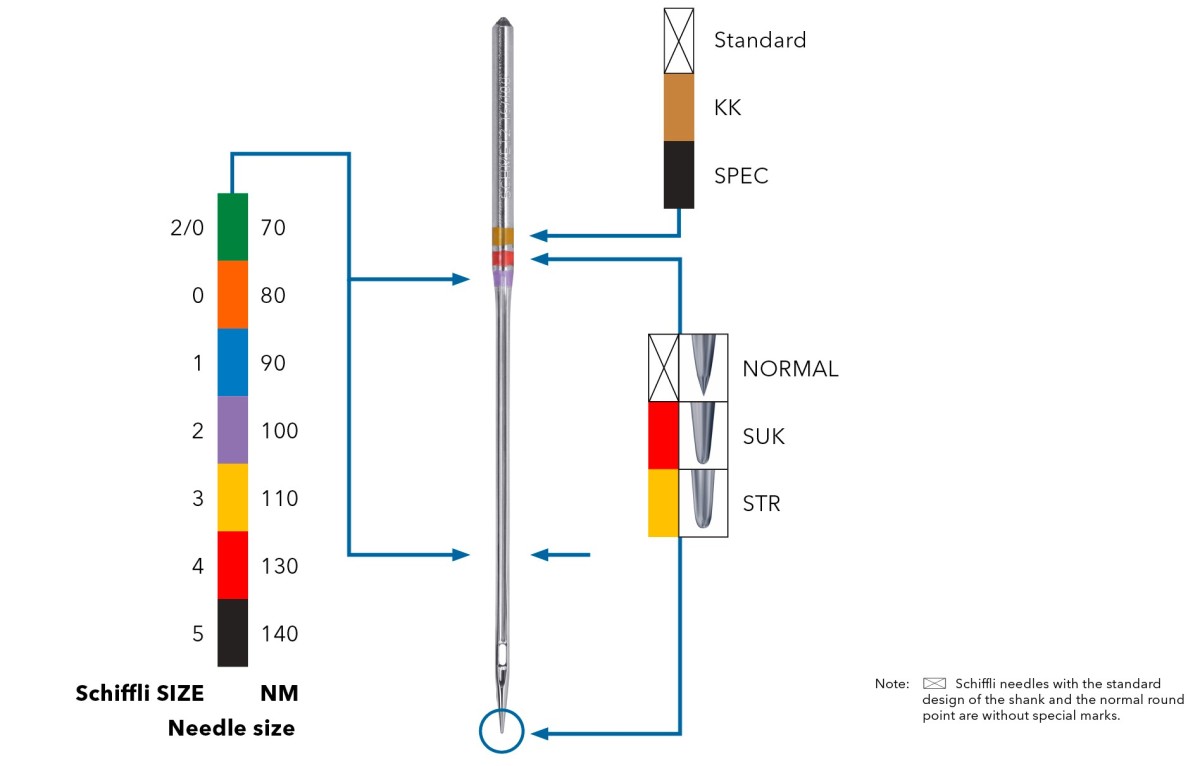
Seen from the tip, the first color marks the needle size. The second color provides information about the point shape. A third color is only added in case of special designs. The standard version and needles with a “normal” point for common, uncritical materials are not specially marked.
The advantages of color coding:
- Rapid identification of needle size and point shape
- Avoiding incorrect selection when changing needles
- Smooth, trouble-free replacement of needles
- High-quality embroidered products
- Economical production
SCHMETZ needles with special geometry SA to work with very heavy or special effect yarns like Lurex.
Needle systems with the additional designation SA indicate needles with an extremely wide eye for very heavy embroidery threads. Compared to the standard eye, the SA eye is approximately 20 % wider.
The advantages of the SA eye:
- Easy threading
- Optimized thread guidance due to less friction
- Reduction of damages to the embroidery thread
- Less thread breakage
- Minimization of repair work
The SCHMETZ solution for repair work in Schiffli embroidery - The 130 N Topstitch and the DBXK5 needle
Even if the greatest care is taken in the production process, there are repeated instances when Schiffli embroidery must be restitched. For example, due to thread breakage during the embroidery process you might face missing stiches and defective Schiffli embroidery appearances.
SCHMETZ 130 N also called Topstitch Needle
The 130 N is usually used in industrially used household machines and has an extra long eye. The eye length of 2 mm stays the same in all needle sizes. The shank is flattened.
The advantages of the SCHMETZ 130 N:
- Long eye for an easier threading of embroidery threads
- Minimized damages to embroidery threads due to less friction in the eye to reduce the risk of thread breakage
- Prevention of thread breakage
- Always exactly the same position of the needle in the needle bar thanks to the flat shank
SCHMETZ DBXK5
The SCHMETZ DBXK5 is normally used in special industrial machines for replacing missing stitches. The eye is 2 NM bigger in relation to the needle size, that means, for example, in an NM/SIZE 70/10 needle the eye corresponds to that of a needle size NM/SIZE 90/14. The needle has a hump between the eye and the scarf and a conical blade.
The advantages of the SCHMETZ DBXK5:
- Larger eye for reduced friction and minimized damages to the embroidery thread
- Minimization of thread breakage
- Reduction of skipped stitches through better loop formation
- Prevention of needle deflection thanks to conical blade, especially with very densely embroidered patterns
- Less needle breakage and thus a longer durability of the needles
- Less downtime for the machines
- Reduction of damage to machine parts such as the tip of the hook and the throat plate
- Very precise border lines of embroidery due to straight penetration
Recommendations for fabrics, sizes and point shapes
Material | Recommended needle size | Recommended point style |
---|---|---|
Gauze/Nonwovens/ Prepared cardboard | NM 70–100 Schiffli SIZE 2/0–2 | R (NORMAL point) |
Woven fabrics made of cotton, linen, polyester or blended woven fabrics | NM 80–170 Schiffli SIZE 0–7 | R (NORMAL point) |
Coarse woven fabrics | NM 80–130 Schiffli SIZE 0–4 | STR (special point for embroidery) |
Fine knitted fabrics | NM 80–110 Schiffli SIZE 0–3 | SUK (medium ball point) |
Coarse knitted fabrics | NM 90–130 Schiffli SIZE 1–4 | STR (special point for embroidery) |
Net fabrics | NM 80–110 Schiffli SIZE 0–3 | STR (special point for embroidery) |
Tulle | NM 80–110 Schiffli SIZE 0–3 | SUK (medium ball point) or STR (special point for embroidery) |
Choosing the suitable SCHMETZ Schiffli needle can help you to avoid or at least reduce the following manufacturing problems in most cases:
Typical Schiffli embroidery problems are:
Material damages
Material damages in the area of the Schiffli embroidery can occur especially with knitted fabrics or thin nonwovens. They are often caused by too thick needles that are used to prevent excessive deflection of the long Schiffli needles. Also the use of unsuitable needle points can lead to problems.
Further causes can be the following:
- Too loosely clamped fabric
- Defective or worn needles
- Damaged embroidery tools, e.g. presser foot, needle plate or shuttle
How you can avoid these damages:
- Adjust the needle size to your fabric.
- Adjust the point shape to your fabric and check the needle point for damages.
- Tighten your fabric and check the tools for eventual damages.
Defective Schiffli embroidery appearance
Defective embroideries appear as follows:
- Only partly embroidered motives due to thread breakage. Different sizes of eyelet holes or defective appearance of eyelet holes due to worn borers.
- Different sizes of eyelet holes or defective appearance of eyelet holes due to worn out borers
- Transverse stripes in Schiffli embroidery
- Shuttle thread visible on the surface
- Distorted embroidery motif
- Undesired puckering in the area of the embroidery
How you can avoid such appearances:
- Change soiled thread spools
- Optimize the thread tension
- Use a thread stop motion to quickly detect the point of breakage
- Examine the borers
- Correct thread guidance
- If you embroider knitted fabric, observe the orientation of course and wale. The weft and warp threads of woven fabric should run at right angles after clamping.
Needle breakage
Needle breakage can cause the following problems:
- Destroyed fabric parts in the area of Schiffli embroidery
- Damages in thin nonwovens
- Mesh damages in knit fabrics
- Needle fragments remaining in the fabric
How you can avoid these problems:
- Adjust the needle size to the fabric to avoid bending and breaking
- Check the needle point for damages regularly
- Check the correct positioning of the needle
- Coordinate the embroidery tools, e.g. presser foot, needle plate, as well as the embroidery thread and material.
- Optimize the thread tension
Skip stitches / Thread breakage
Skip stitches and thread breakage are caused by the following:
- Incorrect thread tension
- Incorrect thread guidance
- Incorrect needle system
- Incorrectly fitted needle
- Use of an oversized embroidery thread in relation to the needle size
- Cloth presser adjustment too high
How you can avoid these problems:
- Adjust the embroidery thread size to the needle size and the fabric, or try a needle with a bigger SA eye.
- Check the correct positioning of the needle
- Optimize the shuttle setting
- Examine the thread guiding elements
- Optimize the thread tension
- Reduce the embroidering speed
- Replace worn out embroidery tools such as thread guiding elements, needle plate and shuttles.
- Optimize the adjustment of the cloth presser